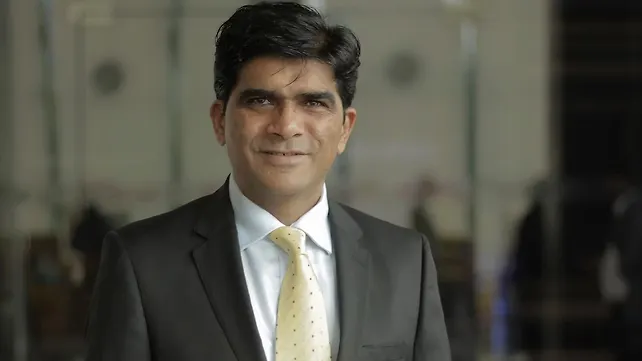
Electric vehicles are not just greener and economical alternatives to internal combustion-powered vehicles but have equally caught everyone's attention by going up in flames and occasionally snuffing out lives too.
While the Centre is amending existing policies to make EVs safer, Rafiq Somani, Area Vice-President, Ansys India, is of the view that vehicle and battery OEMs can leverage simulation in this effort too.
'Physics-based simulation can be used to make EVs safer right from battery and battery management system to how safe they will be if they meet with an accident,' he said.
Software To Hardware Simulation
According to Ansys, most EV fires start from the battery because of thermal runaways. The use of inferior quality wires, battery casings and poor BMS are also other causes for fires. The company claims simulation can be used to run different scenarios a battery would be subject to in real conditions. Based on the findings, OEMs can decide on which materials to replace.
'The beauty of running a simulation is it treats everything starting from wires, circuits, BMS to battery casings equally. Not only can it tell whether all these components complement each other or not, but advanced simulation tools can also suggest alternatives,' Somani explained.
He said driving scenarios that have not happened anywhere in the world can also be simulated to gauge how a BMS will work under the same conditions.
Thermal analysis, cooling systems and structural integrity (including mechanical) are the larger areas that can be made better with simulation. According to Ansys, these can replicate crash tests, climate change and terrain changes in the virtual world.
Increasing Range
Simulation tools can also be used to improve the range of EVs by helping design engineers and OEMs plan better aerodynamic structures. Somani said digital twins technology can be used to test what simulation tools are recommending.
For instance, tests arising out of these tools can suggest where the OEM can reduce weight and areas that need better aerodynamics. Volkswagen's I.D. R Pikes Peak car design team used Ansys' multiphysics simulation involving electrical and thermal parameters to design and validate the battery model. This electric race car went on to smash not only the EV speed record at the track by more than a minute but also the overall record by over 16 seconds.
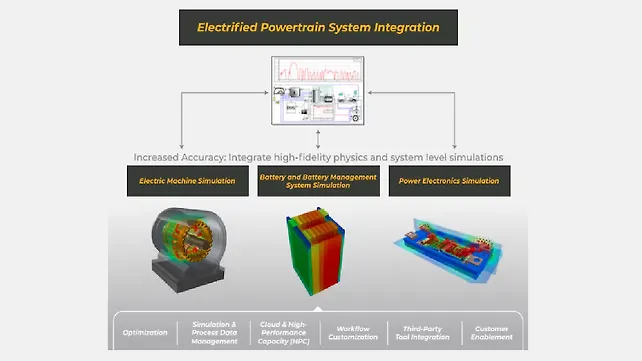
However, speed and range expansion are not the only goals that digital twins and simulation tools can achieve. The reduced weight, in terms of metals used and in terms of battery cells discarded, can lead to lowered production costs for the OEM.
For instance, reducing barely 2 kg of steel from a car chassis will lead to a reduction of 2,000 kg of steel while manufacturing 1,000 cars. Similarly, reducing the battery cell count from 110 to 100 will lead to a reduction of thousands of battery cells when the EV model is manufactured commercially.
Lesser Prototypes
Using these technologies and tools can also help the OEMs save investments in creating prototypes for testing. Somani explained that the modern simulation and digital twin tools can easily replicate real-world conditions, and hence prototypes can be tested virtually.
Citing the case of premium electric maker Lucid, Somani said the company had reduced its cycle time by almost 50% leveraging these technologies. On the availability of data to validate results generated by simulation and digital twin tools, Ansys notes that there is more than enough available in the public domain.
“As more and more vehicles get equipped with sensors and electronics, this data will increase along with the efficacy of these tools. OEMs have also started collecting data from the test cars that they run globally,” said Somani. These tools, states the company, are not limited to EVs and can also be used to make ICE vehicles better.
Also Read